Tin Bread Line
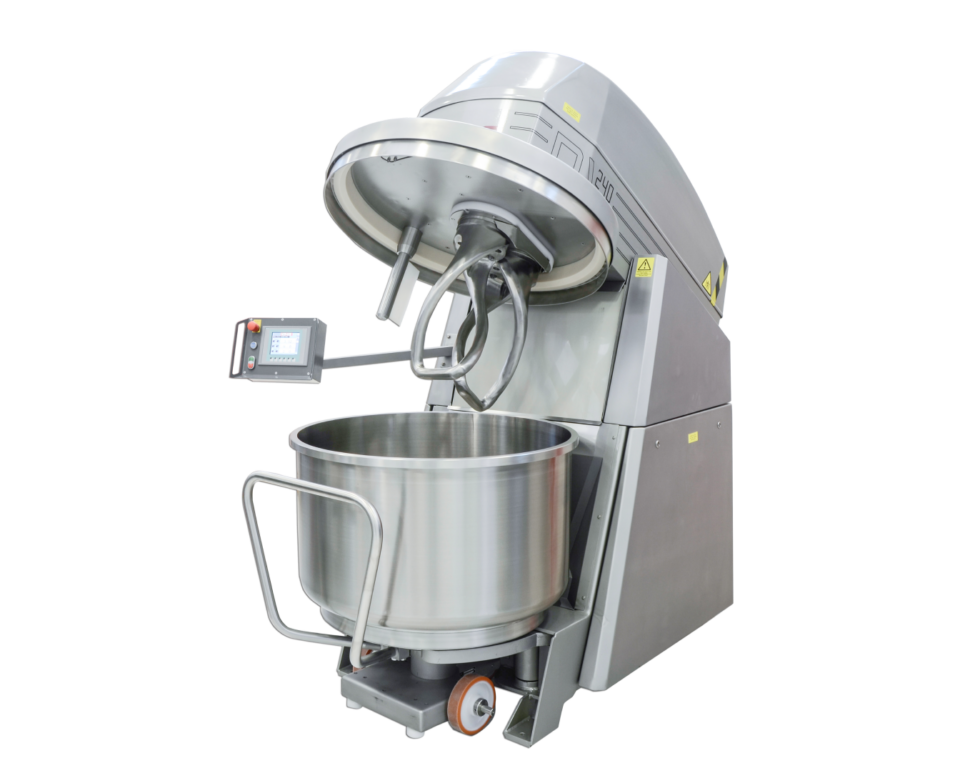
Twin Twist Mixer
Two attachments with unique twisting motion and set at an optimum working angle provide the perfect foundation for the production of dough. A shorter kneading time in addition to more air and oxygen give superb results.
- Dough capacity of 125 kg and 240 kg
- Removable dough bowl
- Two speed settings for the kneading tool and the dough bowl.
- Short kneading times with minimal dough warming
- Hydraulic dough bowl locking
- Hydraulic lifting and lowering of head
- Intensive yet delicate dough preparation (e.g. for fruit dough)
- Optional: Stainless steel base frame and hygienic “H” build type (can be spray cleaned with water)
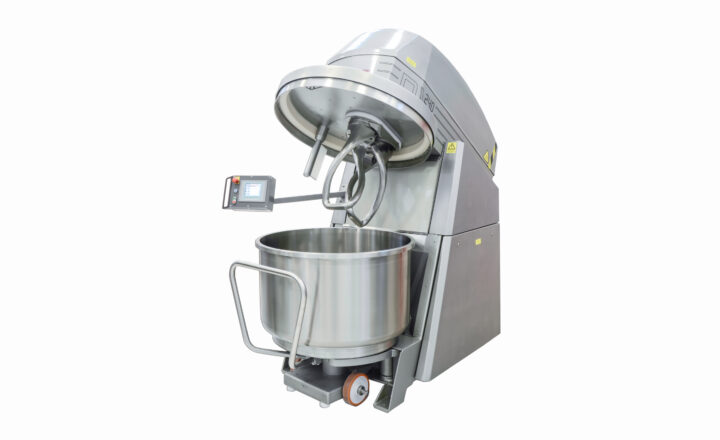
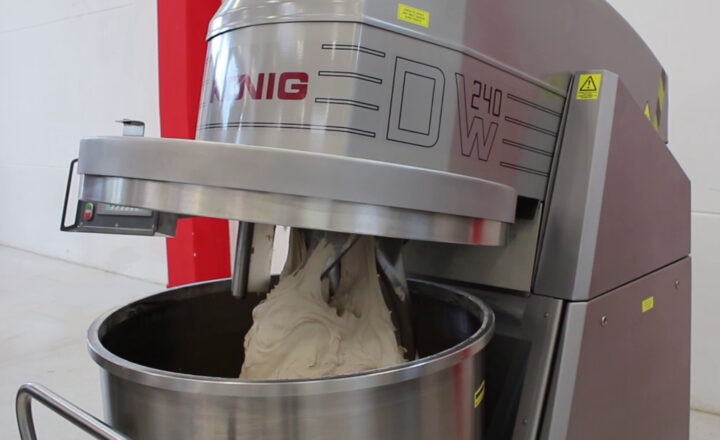
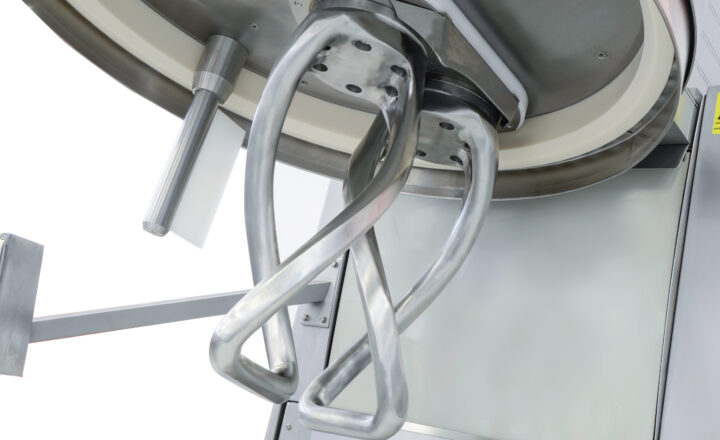
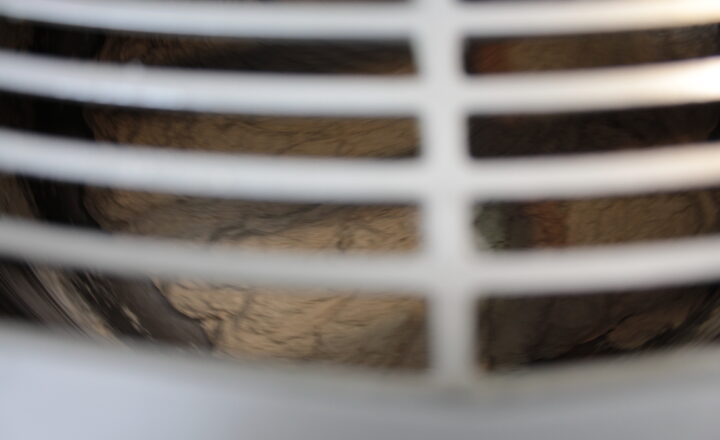
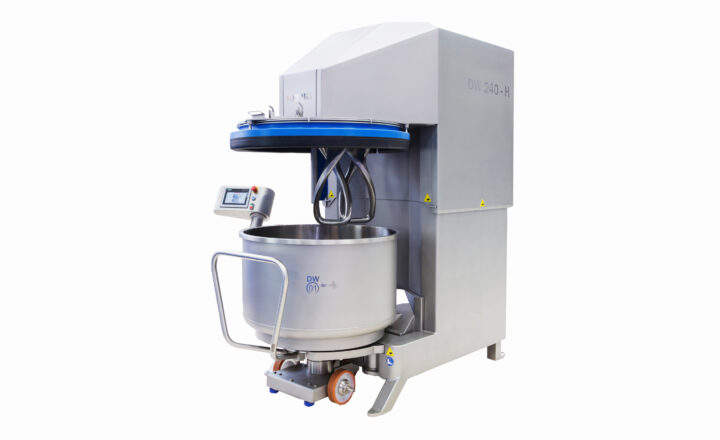
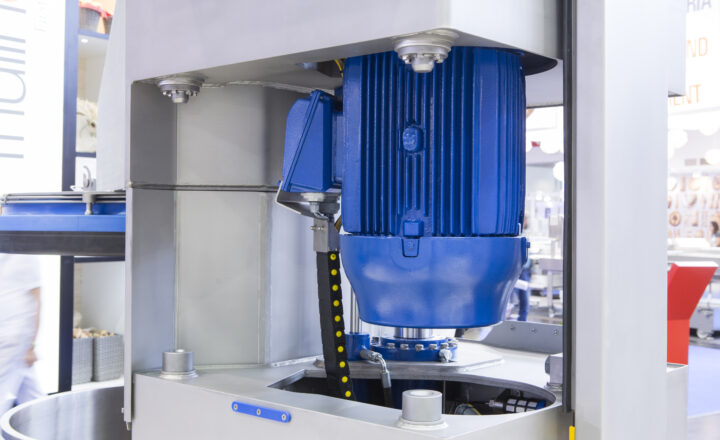
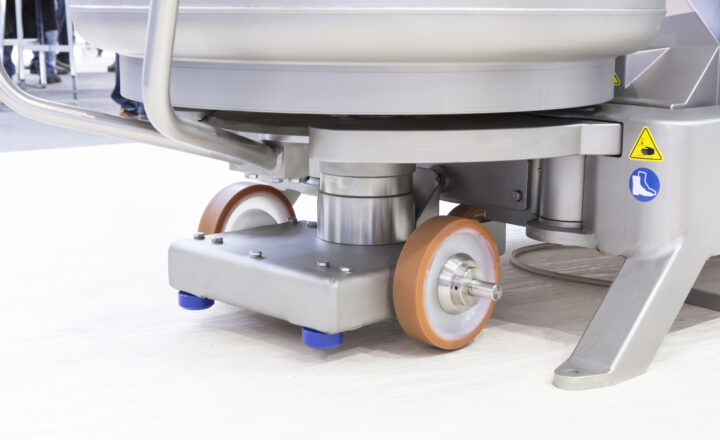
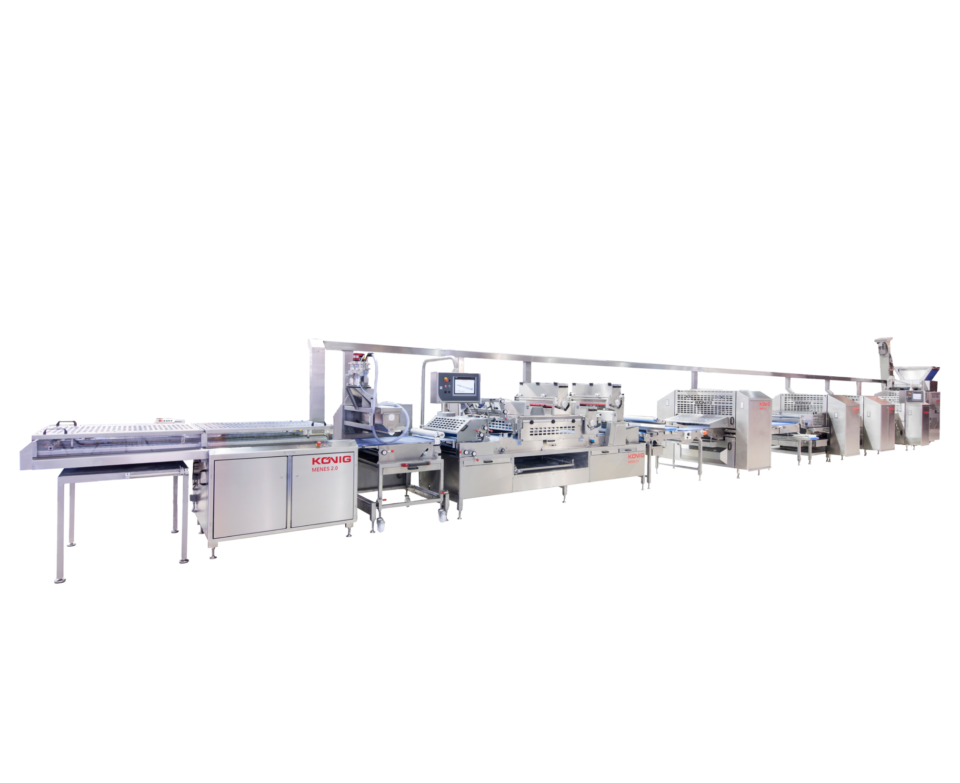
Menes
The Menes dough belt system can be adapted and expanded at any time to meet your requirements thanks to its well-thought-out module concept.
- Dough throughput of 500 to 1,500 kg per hour
- Multiple operational widths (800, 1,000, 1,200, 1,600 mm)
- Dough sheet height from 1 to 50 mm
- Huge range of dough yields (140 to 190)
- Full modularity thanks to the building-block principle
- High product variety guaranteed
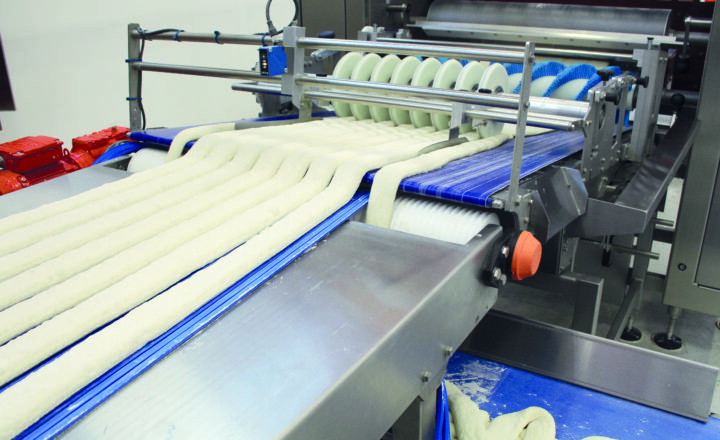
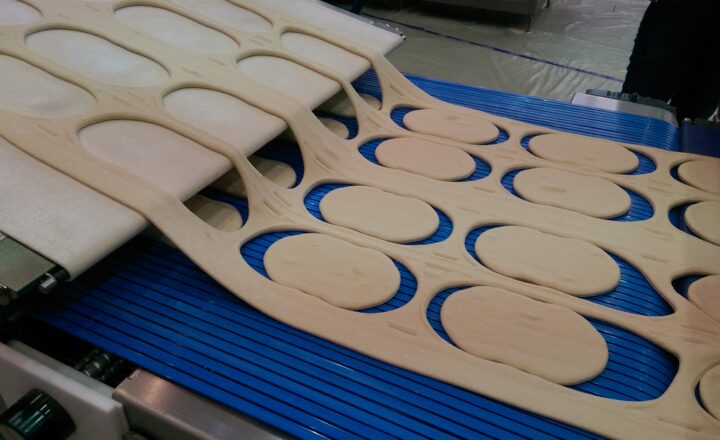
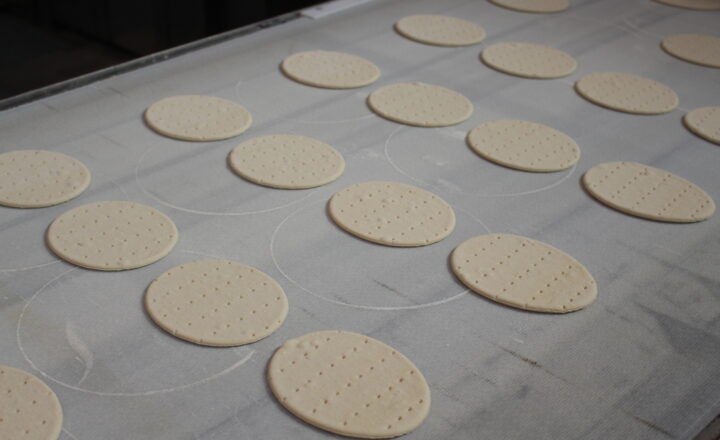
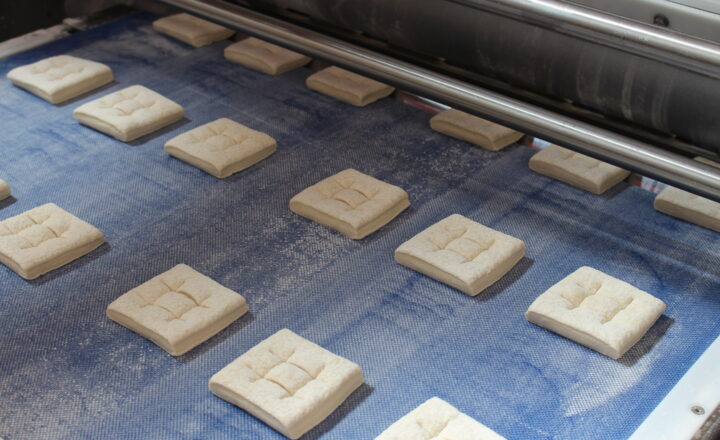
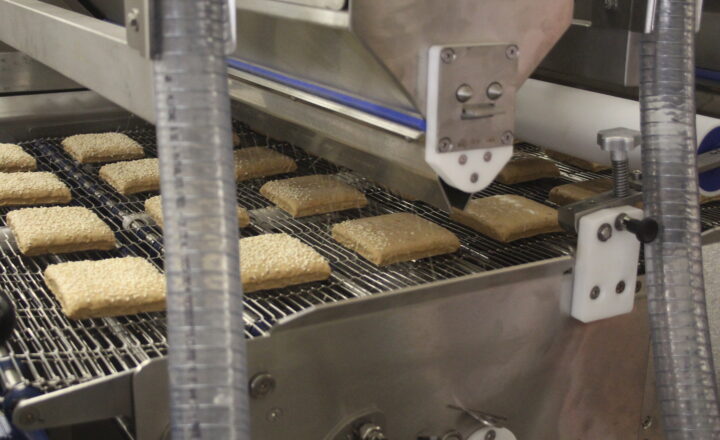
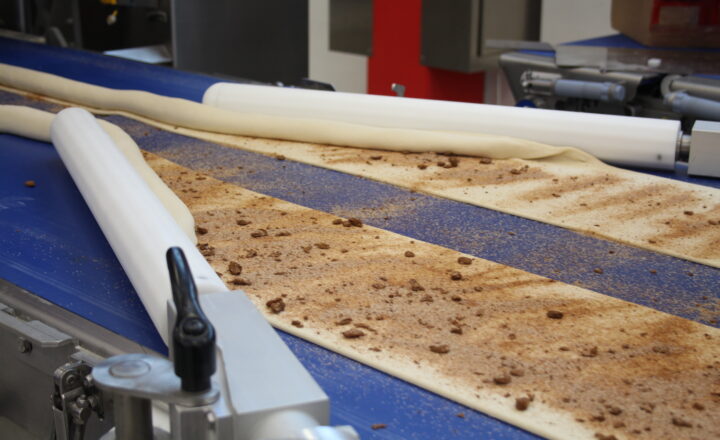
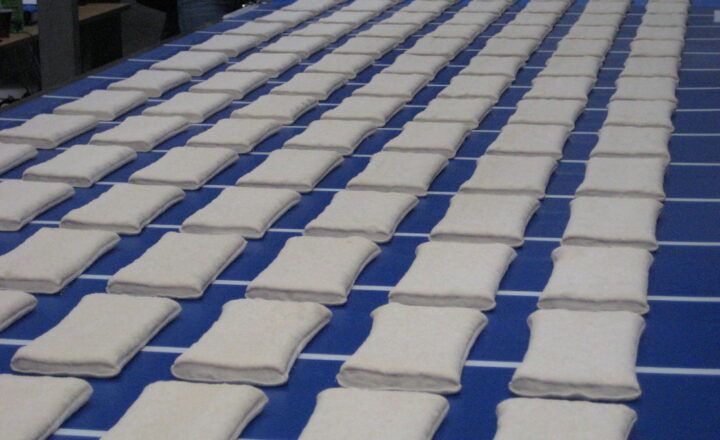
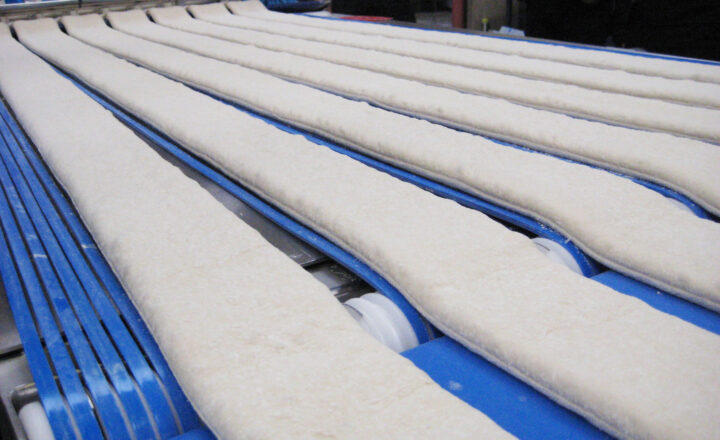
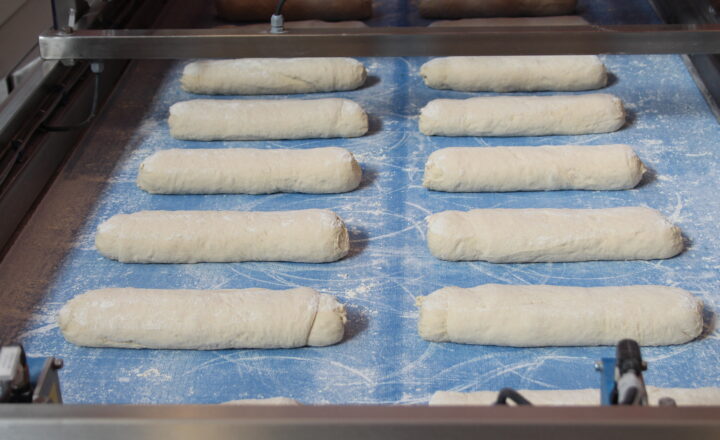
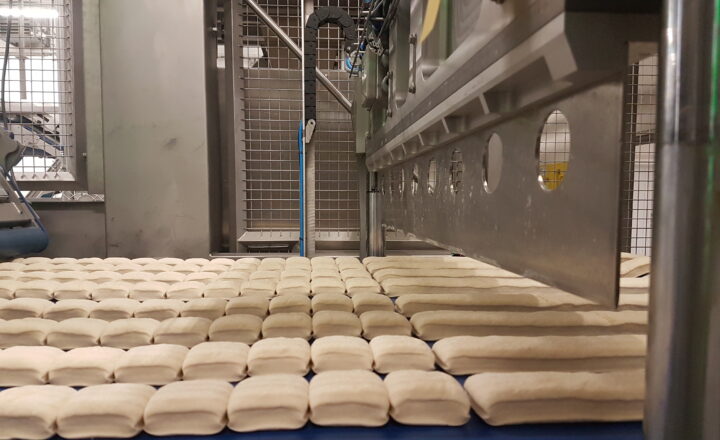
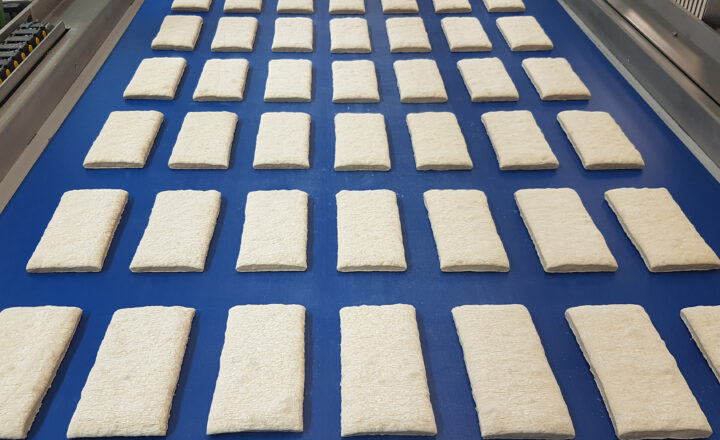
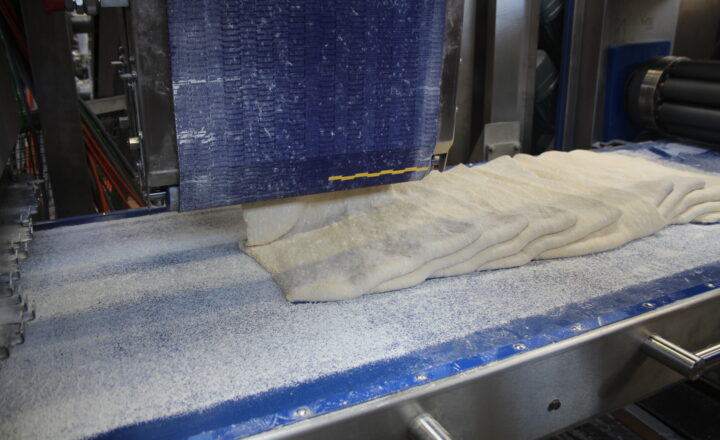
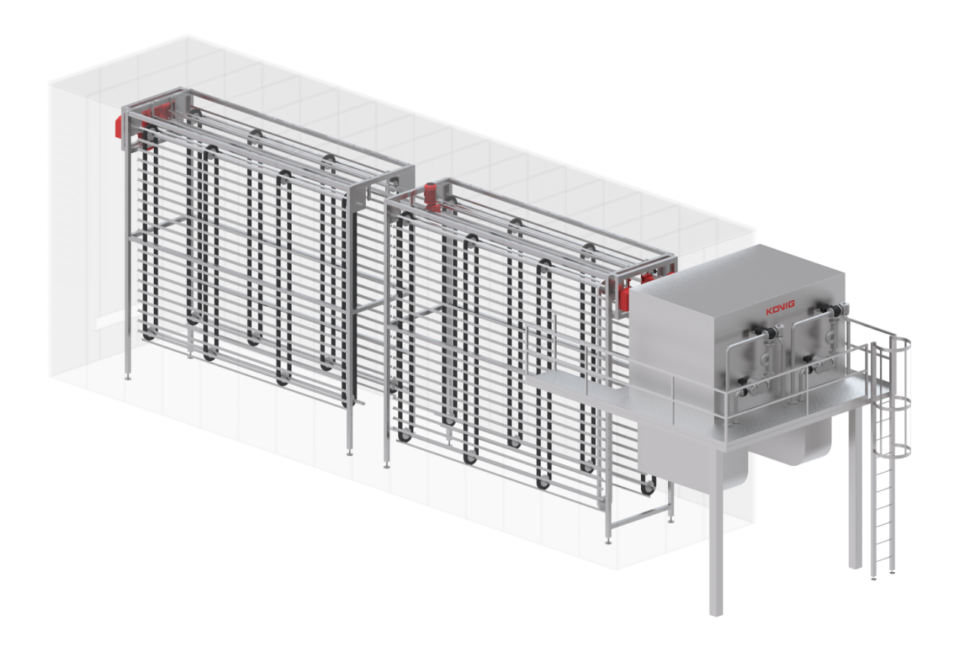
Step Proofing Cabinet
The modular structure of the step proofing cabinet facilitates gentle and even processing of the dough pieces. Its compact and hygienic design and the use of high-quality components ensure maximum efficiency and flexibility in production, and all of this with a reduced need for space. The proofing cabinet is completely enclosed by heat-insulating plates. Nevertheless, all of the mechanical components are fully compartmentalised and thus easily accessible for maintenance work.
The climate control unit facilitates extremely precise control of all proofing parameters (temperature and humidity) and ensures the maintenance of uniform and constant proofing conditions in all areas of the proofing cabinet.
- Suitable for products on / in plates, sheets, or moulds
- Standard operational widths: 800, 1,000, 1,200, 1,600, 2,400 mm
- No capacity limitations
- Various layout combinations
- Modular construction
- Standard version in stainless steel design
- High standard of hygiene
- Adjustable processing time
- High-precision system for the control of heating, cooling and humidity
- The same mechanical construction can be used for coolers, freezers and storage

Transport system
The conveyor system takes moulds and sheets and transports them cyclically to all of the units in the line, starting at dough preparation through to unloading and return conveyance.
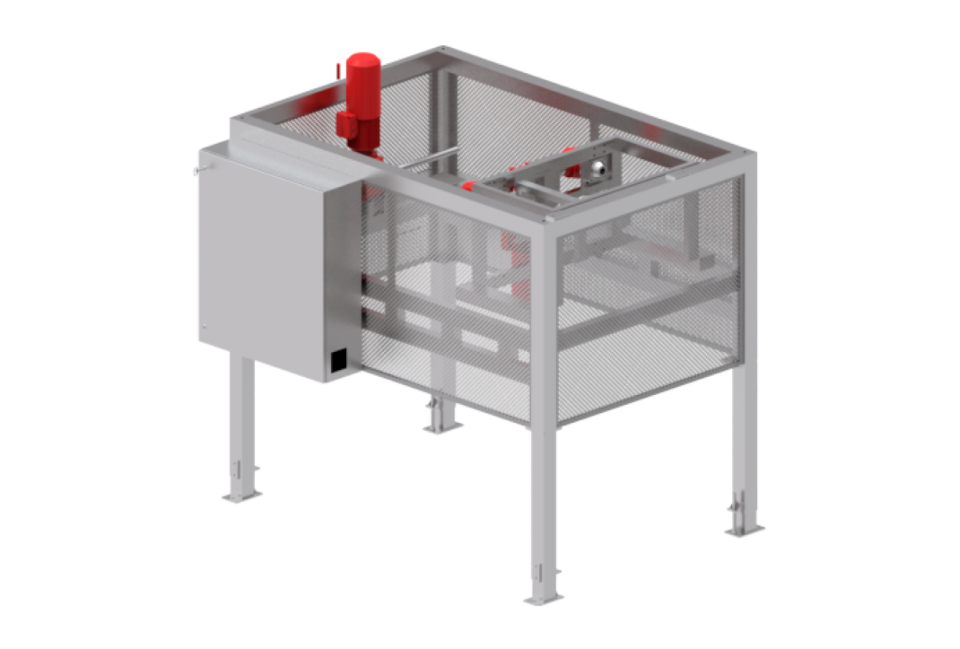
Lidding Unit
The lidding unit takes lids from the lid return unit and places them on the tin bread baking moulds.
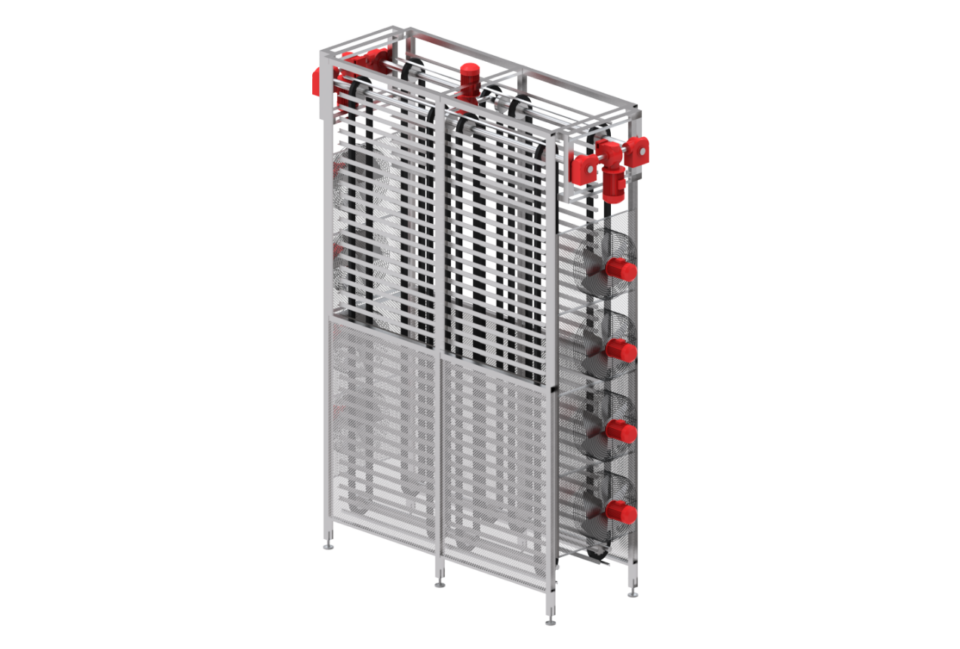
Cooling
The cooling system makes use of the same mechanical and hygienic construction of the step proofing cabinet and ensures that the empty baking moulds are cooled in the right way through the active convection of the surrounding air using several fans. Inside the cooler, the baking moulds are moved using a chain lift system.
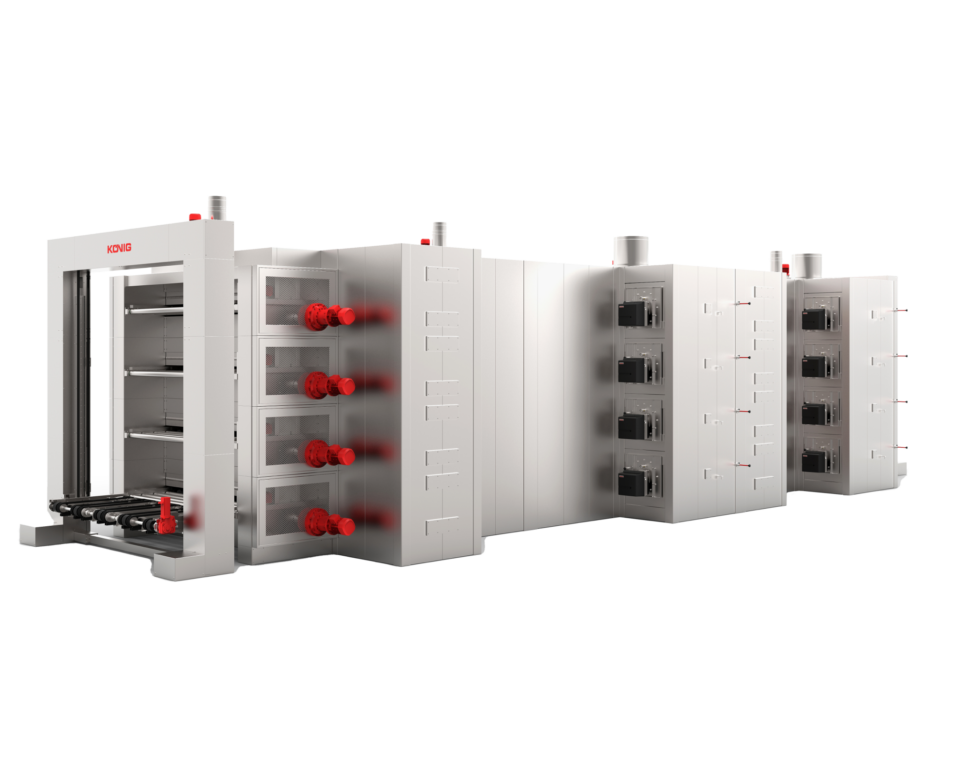
MDI Stratos
The indirectly heated MDI STRATOS multi-level tunnel oven is an extraordinary combination of compact design, modularity, performance and control. The independent levels allow for the baking of different quantities and products.
- Baking surface: 500m2 on up to six levels
- Belt width: 2,500 mm with modular design and small floor area requirement
- The baking process is possible directly on the belt or in the baking mould
- Individual control of heating from the top and bottom
- Integrated cleaning system for belt and baking chamber
- High-speed lifts for feeding and unloading
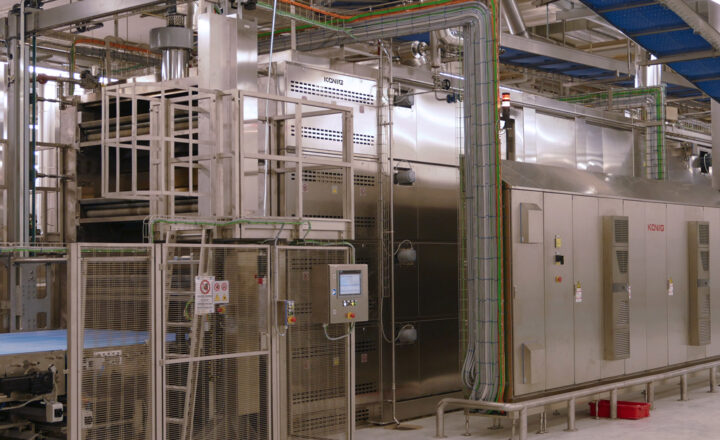
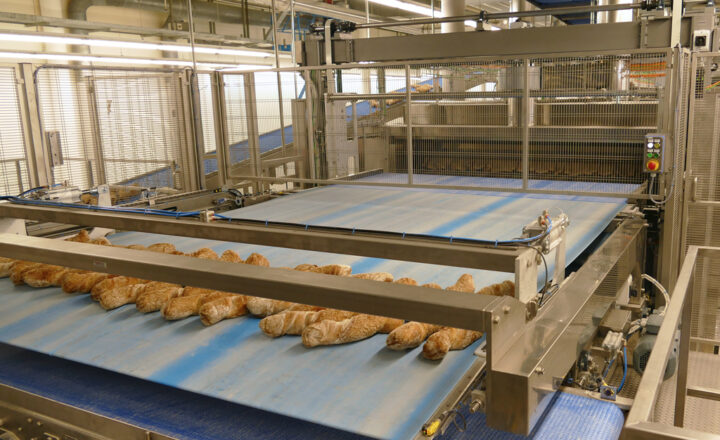
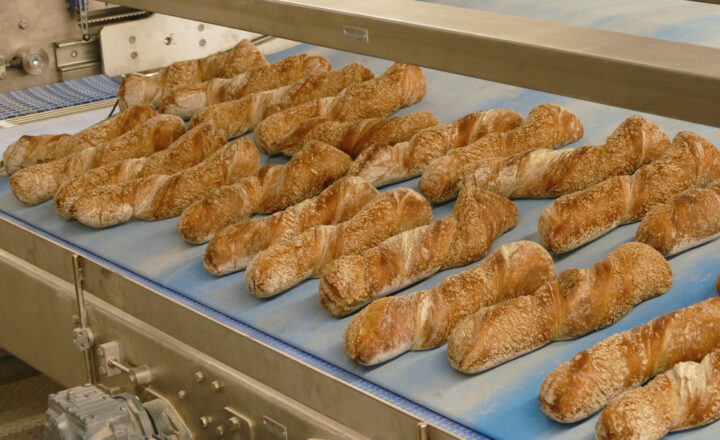
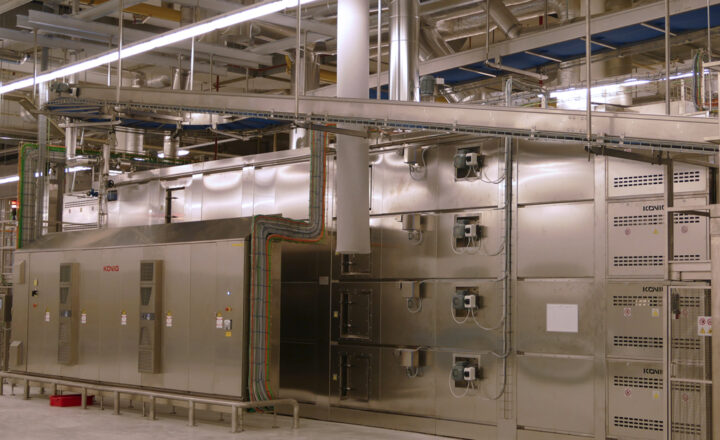
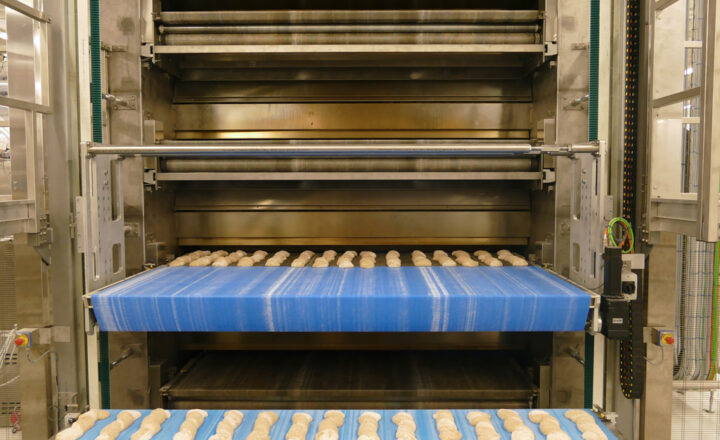
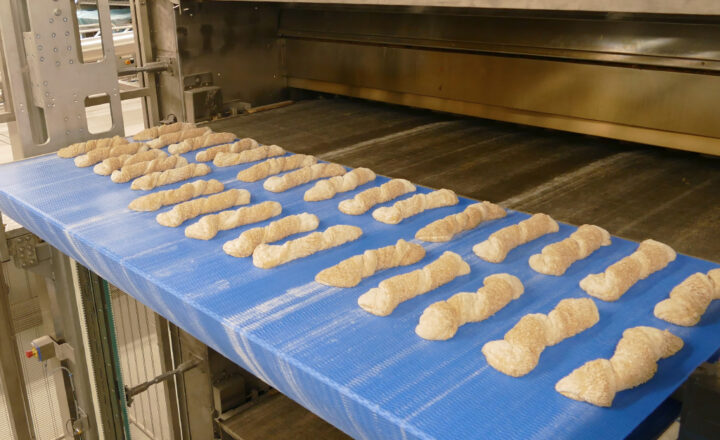
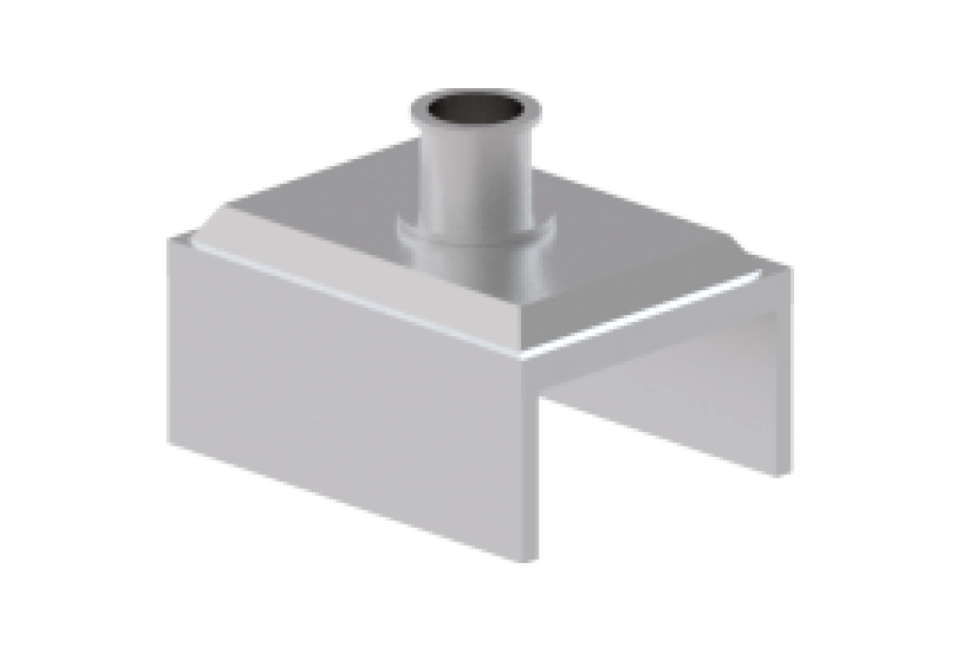
Baking Mould Cleaning Unit
The baking mould cleaning unit cleans the baking moulds after the product has been removed and vacuums off any soiling.
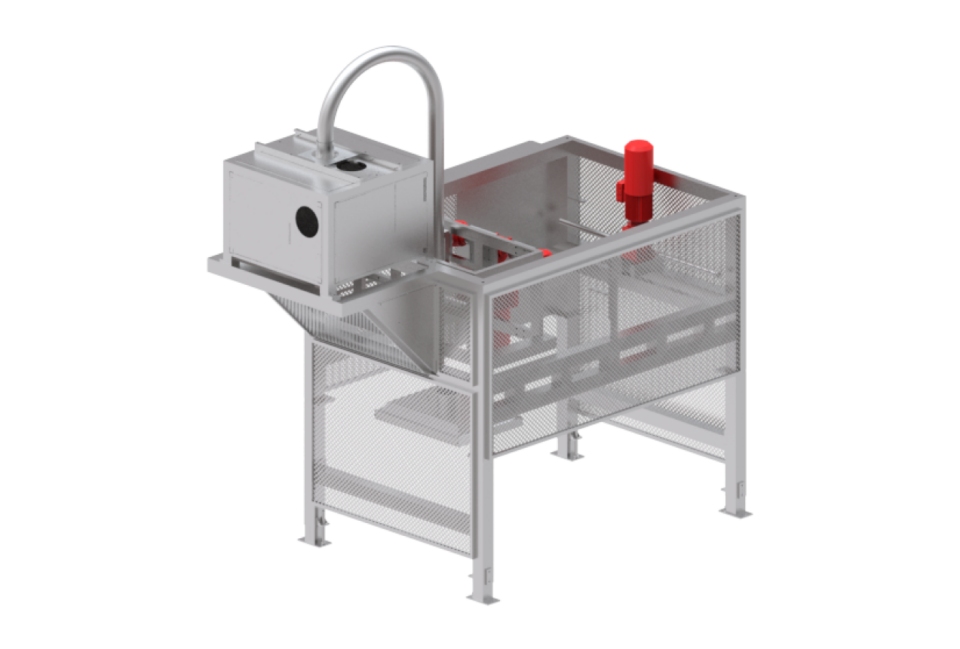
Baking Mould De-Panning Unit
The baking mould de-panning unit empties the products from the tin bread baking moulds using a scraper head with needles or suction cups and positions them on the conveyor belt ready for the spiral cooler.
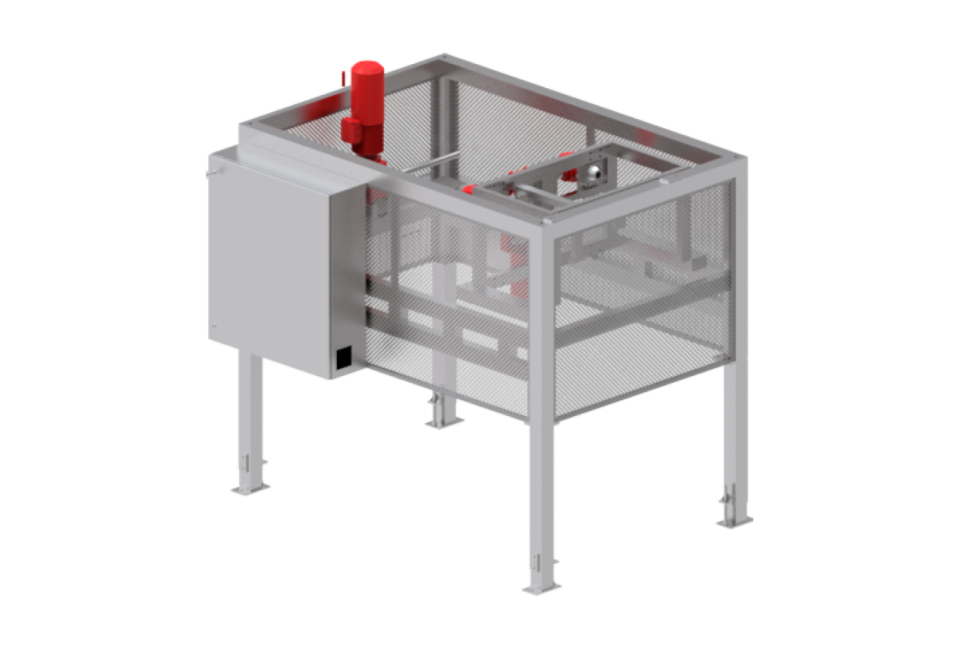
De-Lidding Unit
The de-lidding unit removes the lids from the tin bread baking moulds and positions them on the lid return unit.

Cooling Spiral
The Koenig cooling spiral ensures optimal and correct cooling of your products thanks to conditioned air.
- Ensures cooling process with the help of air conditioning
- Direct transfer to the packaging conveyor
Automatic temperature adjustment (zone control) - Stainless steel structure and frame
- PLC control
- Insulation by sandwich panels
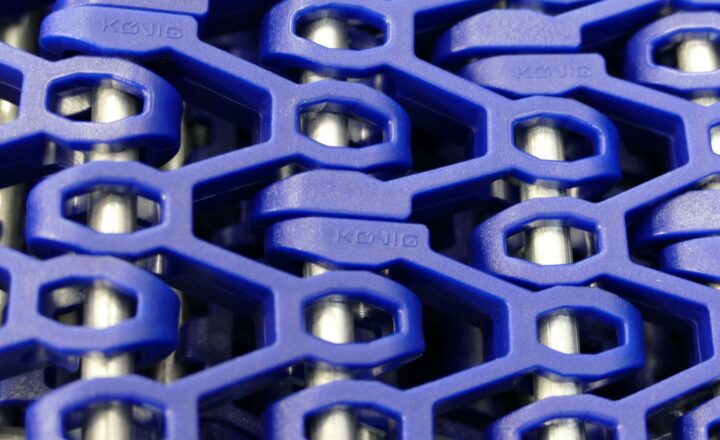
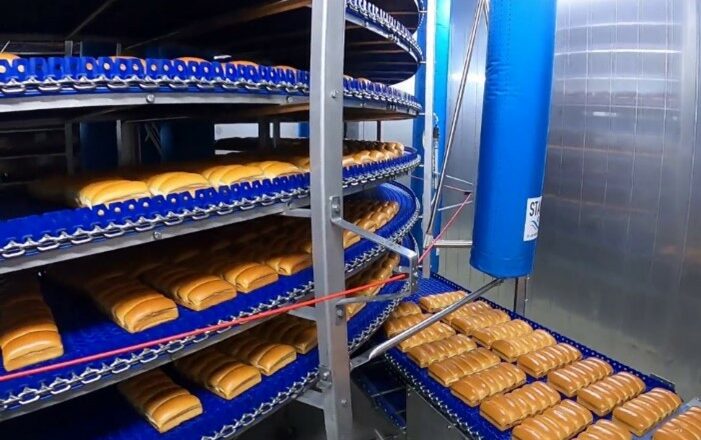
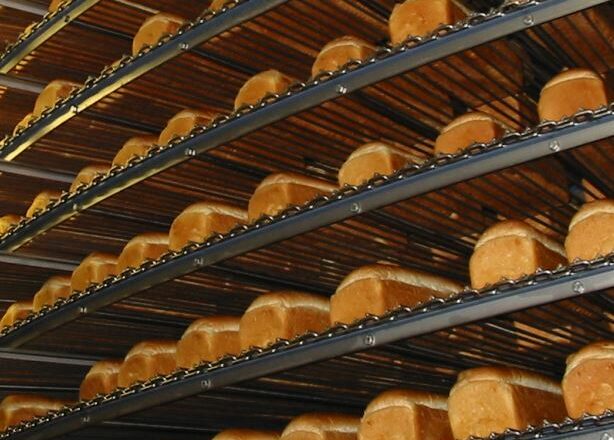
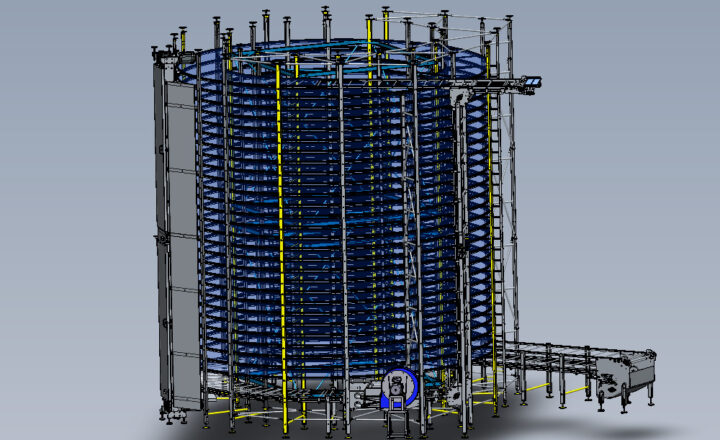
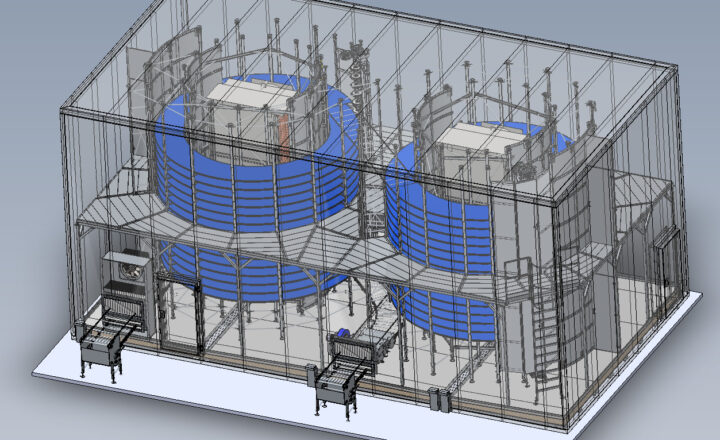
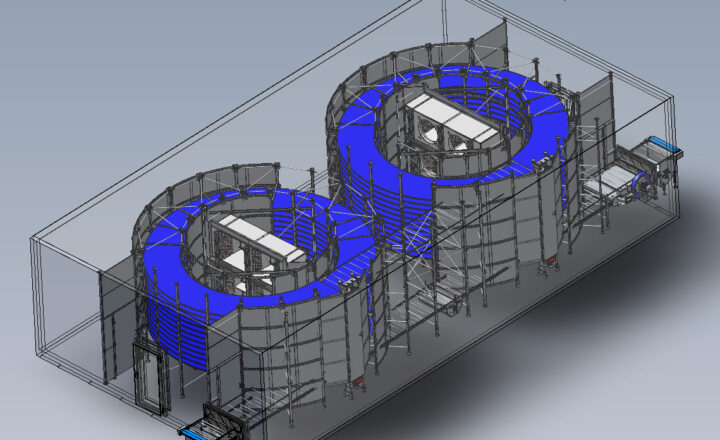
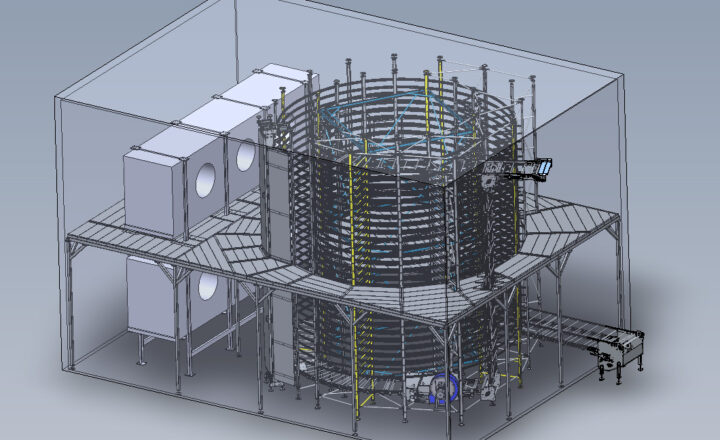